日本盛(本社・兵庫県西宮市 森本太郎代表)は、食品安全・品質管理にかかわる報告業務をDX化により、年間500時間(2024年9月現在)の業務負担削減を達成した。今後、設備維持管理業務を含め報告業務の全行程をDX化し、年間1000時間の削減を目指す。
同社が導入したのは、カミナシ(本社・東京都千代田区 諸岡裕人代表)のカミナシレポート。クラウドベースの現場管理DXプラットフォームで、タブレット端末を用いて記録表記入などの報告業務を行う。
システム開発の専門知識を持たない社内担当者でも直観的な操作でアプリ開発を構築でき、利用する作業員から使用上の要望や修正点があれば、即日反映させることができるなどの特長を評価し導入に至った。
同社本社工場でアプリ開発に携わる生産部課長補佐清水淳司氏に、導入の経緯と導入後の作業環境の変化などについて聞いた。
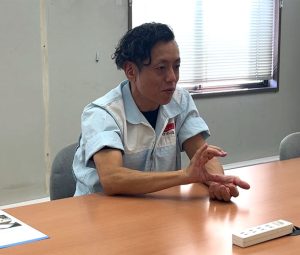
――導入の経緯をお聞かせください。
清水 食品安全マネジメント規格「JFS-B規格」の認証を取得後、報告用の書類作成にかかる作業が膨大なものになった。紙ベースの業務遂行に限界を感じたことがきっかけ。導入後、食品安全管理にかかわる作業量は、認証取得以前より減っている。
――アプリ導入後の監査関連業務で最も大きな変化は。
清水 定期監査で手書き資料を紙ベースで提出すると文字が読めない、記入ミス、チェック漏れやチェックミスなどで再提出となり、作業負荷が大きかった。導入後はそうした問題はなくなり、記入ミスがないので監査担当官とのコミュニケーションも円滑になった。
――社内でアプリ開発について、使用感は。
清水 クイズやアンケートに答えていくような操作感で構築できる。開発に迷うことはほとんどない。運用後も現場の作業員とやり取りしながらその場で問題点を訂正でき、新規項目も即日追加できる。システム提供元の技術者にサポートしてもらうケースも少なく、効率的でストレスフリーな運用ができている。
――運用後の作業現場の効率化について具体的な事例をお聞かせください。
清水 定時の報告業務も、工場内の作業の進捗状況がリアルタイムで確認できるので、チェックミスやロスがなくなった。仮にミスが生じてもすぐに担当者に連絡して解消している。工場内に建屋が3つあり、すべて歩いて見て回る時間がないので助かっている。
また新規作業員への作業内容の説明、人材が入れ替わった際の引継ぎ業務などもほとんど必要なくなった。
例えば製造ラインで逸脱などがあった場合の報告でも、アプリ画面には、トラブル発生時の対応方法や、次に必要とされる作業内容がロールプレイングゲームのように表示される。現場責任者が作業員にやり方を説明する手間もかからない。
海外向け商品のラベル印刷など賞味期限の日付表示は国によって記載方法が異なるが、作業員が作業内容を写真で送ってくるのでリアルタイムで正・不正の確認ができる。
――作業負荷軽減以外のメリットは。
清水 当社ではないが、食品製造現場では異物混入の可能性を極限まで減らしたい。現場における紙の使用はこの観点からもなくしたかった。また顧客など外部からの依頼で、過去のトラブル情報を調べる必要が生じた場合でも、必要な情報に素早くアクセスできるようになり、外部評価が高まった。
現在、製造ラインの報告業務の70%程度をカミナシで運用している。今後未導入の箇所や設備維持管理などの業務にも導入し、工場内の100%DX化を進めていく。