20年春に第二ライン稼働予定 輸送・製造コストとCO2排出量を削減
ペットボトル(PET)メカニカルリサイクルのプロセスは以下の通り。
①回収PETを粉砕してフレーク(薄片)にする。
②そのフレークをアルカリ洗浄して表面を削り取り高度化リサイクル用フレークにする。
③高度化リサイクル用フレークを高温・真空下にさらして樹脂に染み込んだ汚染物質を吸い出して徹底的に除去する。(溶融・メカニカル処理)
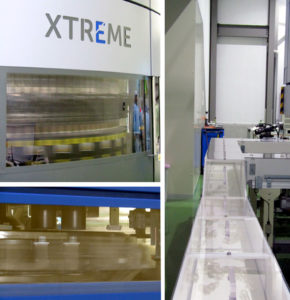
④メカニカル処理された非結晶レジンを結晶化させる。(結晶レジンペレット)
⑤結晶レジンを再び溶融してPETのもととなる試験管のような形をしたプリフォームを成形する。
⑥プリフォームを加熱し高圧空気を吹き込んでPETに加工する。
◇ ◇
サントリーホールディングスは昨春、このプロセスの一部(主に③、④)を省くことで環境負荷低減と再生効率化を実現する「FtoPダイレクトリサイクル技術」を協栄産業、伊・SIPA社、豪・EREMA社と世界で初めて共同開発した。
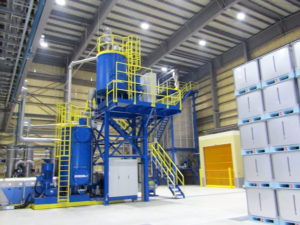
3月29日、協栄産業の「東日本FtoPファクトリー」(茨城県笠間市)で開かれた説明・見学会で協栄産業の古澤栄一社長は同技術について「フレークを溶融してペレット(レジンペレット)にし、ペレットを溶融してプリフォームをつくる。この2回の溶融を1回にすることで、従来の仕組みと比較し輸送・製造コストを削減し、CO2排出量を約25%削減する」と説明した。
東日本FtoPファクトリーには、同技術を実現したFtoP製造ライン(第一ライン)が昨年8月に稼働し、20年春には第二ラインの稼働を予定している。
1ライン当たりの年間プリフォーム製造能力は約1千200万ケース分のPETに相当する3億本。東日本FtoPファクトリー全体の処理能力は年間3万tで「FtoP製造ラインにすると7台分くらいの量。まずはFtoP製造ライン2台で処理し、2台で処理しきれない分は違う工場に輸送しペレット化していく」。
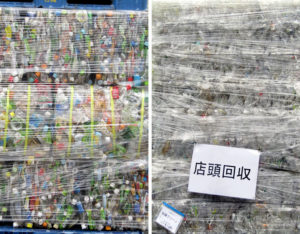
消費者に求める正しい分別
①キャップをはずす
②ラベルをはがす
③中を水洗いする
④つぶす
――が正しい分別。
東日本FtoPファクトリーでは、
①スーパーやコンビニなどの店頭で回収された事業系PET
②市町村で回収された自治体系PET(容器リサイクル法ルート)
③自販機で回収された事業系PET
――の主に3種類をリサイクルしている。
「店頭回収はポイントがもらえるからきちんと出す。自販機の脇で回収したPETはキャップもラベルもほぼフルについている。同じ人でも、出す場所によって、これだけ違うと思ったほうがよいのかもしれない」とみている。
同ファクトリーの回収PETを選別・破砕・洗浄・乾燥する処理能力は1日350~400本で、敷地内には2、3週間分の回収PETが堆く積まれている。
回収PETをフレークにするプラントでは、選別・破砕・洗浄を行い、加水分解で表面の汚れを徹底的に除去したフレークにする。このフレークにするまでのプラントとFtoP製造ラインのプラントはパイプでつながれ、パイプから運ばれるフレークが高温・真空下で一定時間処理され溶解後、直接プリフォームが製造される。
高度と水の沸点の関係は、高度が上がるほど水の沸点は低くなる。水の沸点は海面(高度0m)で100℃、富士山山頂(3千776m)で87.8℃、宇宙との境界線(100㎞・カーマンライン)で-16℃となる。
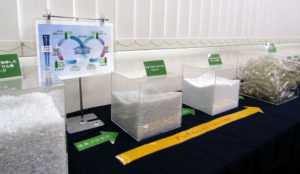
フレークはまずEREMA社の押出機に投入され、そこで上部と下部の2つのリアクターで順番に高温・真空下で一定時間処理することで物性を回復。「上空100㎞以上の真空では-20℃で水が蒸発する。そこを200℃にすることで地球上にある化学物質が揮発する仕組みを利用している」という。
溶融されたフレークはフィルターで濾過され、SIPA社のプリフォーム成形機に送り込まれる。同成形機では無菌充填用の15gのプリフォームを成形し、すべてサントリー食品インターナショナルに納入されている。成形速度は1分間当たり約820本で年間に最大3億本を成形している。
ボトルtoボトルの水平循環型リサイクルは、理論上、何度でもリサイクルできる仕組みになっている。
「IV値(粘度)0.8のバージン原料がボトルになると粘性が落ち0.74や0.73になる。それを洗浄して加水分解し、分子を再度上昇して(再縮合重合反応)0.8に戻す。極端にいうと、その繰り返しで何度でも使える」。
ただし課題もある。同席したサントリーMONOZUKURIエキスパートの高田宗彦チーフスペシャリストは「不純物が混ざってくると、どんどん濃度が上がっていくので、ボトルtoボトルを続けていくのは難しいと思うが、全PET重量の50%程度であれば新しい血(バージン)も入るので可能となる。不純物の濃度がどこまで上がっていくかも、やってみないとわからない」と指摘した。
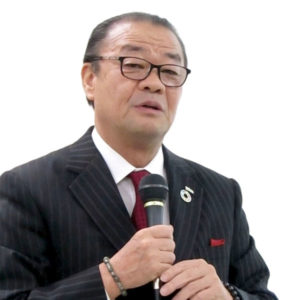
協栄産業は「分ければ資源、混ぜればゴミ」を企業理念に掲げ、古澤栄一社長が29歳の85年に創業。古澤社長は「きっかけは79年に『ジャパン アズ ナンバー1』と言われながらオイルショックが起きたこと。大量生産・大量消費・大量廃棄が進む中、このまま何もしないでいると石油が枯渇すると考え、自分にできることはないかということで最初は1人で孤軍奮闘した」と振り返った。
現在は、協栄産業グループで売上高100億円強、従業員400人。主要工場は、廃プラスチックの一次処理工場の栃木工場、多用途向けリサイクルPET樹脂工場の小山工場、ボトルtoボトル専用工場のMRファクトリー、そして今回の東日本FtoPファクトリーの計4つとなる。グループ全体では全国に8社26拠点11工場が点在している。